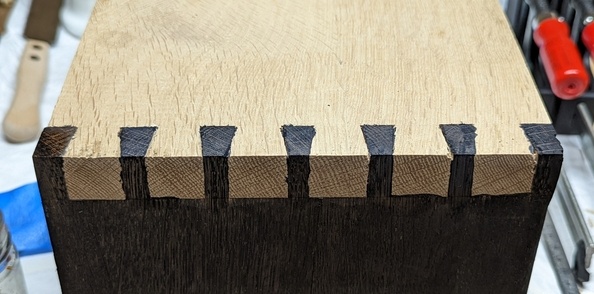
Je cherche à développer l'usage de l'ébonisation des bois tanniques dans mes réalisations, afin de mettre en valeur certains assemblages, introduire des contrastes avec un bois unique, mais aussi répondre à des problématiques techniques liées à l'usage des surfaces traitées.
Qui dit bois identiques et traitements de surface différents, dit difficultés à délimiter précisément la frontière entre les pièces de couleur différente au long des étapes d'ajustement, puis de finition proprement dite.
Il importe donc de définir un processus optimal de traitement des surfaces afin d'obtenir au final à des pièces intriquées mais clairement délimitées, lisses et protégées.
Les essais développés par la suite visent cet objectif. Il est probable que les conclusions s'appliquent aussi à des teintes à l'eau, mais le périmètre de ce pas-à-pas se limitera aux tests réalisés en matière d'ébonisation.
Le support de ces essais est un meuble en cours de fabrication, dont 3 assemblages sont réalisés par queues d'aronde. À ce titre, 3 processus de finition seront testés, avec une finition huilée au final.
Liste des articles
- Les supports de tests
- L'ébonisation
- La méthodologie de test des différents protocoles
- Assemblage A : pinceau sans protection
- Assemblage B : ébonisation avec délimitation par scotch
- Assemblage C : Huilage sélectif avant ébonisation
- Bilan comparatif
- Discussion autour de la place du collage dans le protocole
Les supports de tests
Voici pour commencer les supports de ces essais : 3 séries de queues d'aronde.
Mes 3 premières, taillées aux outils à main : soyez indulgents, j'aborderai l'impact de ces imprécisions sur le processus de finition
Pour commencer, voici la première série que je nommerai assemblage A par la suite.
Assemblage à blanc avant collage et reprise au rabot/ponçage
Voilà la deuxième série réalisée chronologiquement, que j'appellerai assemblage B.
Même condition : assemblage à blanc, sans collage ni rabot/ponçage
L'idée de la création de ce pas-à-pas m'ayant été soufflée en cours de projet, je n'ai pas de photos de l'assemblage C à l'état brut. Il est néanmoins comparable à l'assemblage B, que ce soit en nombre de queues comme en précision de l'assemblage.
Le bois utilisé pour ces assemblages est du chêne, issu d'une forêt en Charente donc ayant poussé sur sol très calcaire. L'espèce exacte est inconnue (forêt abattue dans les années 1950)
L'ébonisation
Le sujet a été amplement détaillé par meilleurs que moi, je me contenterai donc d'un rapide résumé du processus à l'œuvre.
L'ébonisation est le résultat d'une réaction chimique faisant réagir les tanins du bois en présence d'acétate de fer appliqué en solution aqueuse.
Le résultat fait virer la teinte à un quasi-noir sur les bois très tanniques, ce qui donne son nom (ébonisation = transformation en ébène)
La réaction se produit rapidement, mais uniquement à l'interface entre la pièce et la solution aqueuse, c'est à dire à sa surface.
Pour des raisons de déformation de pièces déjà stabilisées et assemblages taillés, je n'explorerai pas ici (au moins dans un premier temps) les processus d'ébonisation par immersion ou par imprégnation sous dépression ("sous vide").
La solution d'acétate de fer sera ici appliquée au pinceau.
En pratique, on obtient cette solution d'acétate de fer en oxydant du fer dans une solution d'acide acétique. En langage commun, on dissout de la laine d'acier/paille de fer/vieux clous/n'importe quelle pièce en acier non inox dans du vinaigre.
Plus l'acide est fort, ou plus la surface de contact de l'acier avec l'acide est importante, plus la réaction est rapide. Autrement dit, pour un résultat rapidement utilisable, utilisez de la laine d'acier la plus fine possible.
La méthodologie de test des différents protocoles
Je dispose de 3 assemblages pour tester différents protocoles. Ça fait un peu juste pour un plan d'expérience digne de ce nom. Je dois faire un choix de protocole pour chacun.
Après discussion avec plusieurs boiseux, j'ai choisi de tester les protocoles suivants :
Points communs : les pièces sont poncées au 120 puis ébonisées hors zone d'assemblage, en 2 couches avec égrenage intermédiaire (car la solution d'ébonisation est aqueuse et relève les fibres)
Les assemblages sont collés, ajustés et poncés après ébonisation des pièces, ce qui a pour effet de retirer l'ébonisation sur une zone dépassant largement l'assemblage proprement dit.
Assemblage A : ébonisation de l'assemblage au pinceau à main levée, sans protection, puis huilage de l'ensemble des pièces+assemblage
Assemblage B : ébonisation de l'assemblage au pinceau, avec délimitation des pièces au scotch de peintre, puis huilage de l'ensemble des pièces+assemblage
Assemblage C : huilage sélectif de la pièce non ébonisée, avec délimitation au scotch de peintre de bureau, puis ébonisation de la pièce concernée et enfin huilage de cette seule pièce.
Assemblage A : pinceau sans protection
On commence par la version sans filet !
L'idée sous-jacente est que l'assemblage A est assez imprécis, avec des jours dans les queues d'aronde, et que le changement d'orientation du fil du bois devrait former une barrière naturelle à la propagation de la teinte.
Vérifions ça en pratique !
D'abord, l'outil utilisé : le pinceau
Ensuite, le collage et le rabotage/ponçage de l'assemblage. J'ai protégé les pièces avec du scotch de peintre pour éviter les bavures de colle, et déjà un premier enseignement : le traitement de surface adhère à l'adhésif.
Pas de très bon augure pour la suite...
Ensuite, ébonisation de la pièce au plus proche des queues, en essayant de ne pas déborder le trait : ça va globalement bien
Ensuite, on commence le dur : badigeonner les extrémités en bois de bout, avec un pinceau trop large qui a des poils qui partent de travers, et déjà les premiers pâtés !
Et ça continue avec les parties en bois de fil !
Pour visualiser l'ampleur du problème, imaginez qu'on peint à l'encre de Chine : indélébile !
La solution retenue pour rattraper le coup a été de jouer du ciseau : la teinte étant uniquement présente en surface, j'ai légèrement creusé les limites entre pièces, soulignant ainsi l'assemblage au toucher.
Ça fonctionne pas trop mal, même s'il faut faire des compromis.
Bilan de la phase d'ébonisation sélective :
Plutôt galère, pour un résultat pas terrible. Une grande partie du problème vient du pinceau utilisé, tout à fait quelconque. Un pinceau d'artiste peintre, avec une vraie pointe, permettrait d'obtenir un résultat satisfaisant au prix d'une certaine minutie.
En termes de temps, l'absence de protection en fait gagner "beaucoup" en proportion, mais qui est perdu par la reprise des bavures. C'est donc un protocole inadapté pour un professionnel (exigence de rendement et de qualité/reproductibilité du résultat), mais on pouvait s'en douter.
Après dépoussiérage général et huilage, aucune bavure des surfaces ébonisées sur les surfaces vierges adjacentes n'est à déplorer.
Le résultat esthétique est satisfaisant pour un œil non averti.
Assemblage B : ébonisation avec délimitation par scotch
Pour l'assemblage B, on repart d'un collage suivi d'un rabot/ponçage pour partir sur une base saine.
se retrousse les manches pour délimiter précisément les limites de pièces
Puis on sort son plus beau bistouri (en l'occurrence un cutter) pour découper précisément le scotch de protection afin de délimiter les frontières entre pièces.
L'idée, comme pour la peinture, est que le scotch empêchera la teinte de passer en-dessous. Comme pour la peinture, je m'attends à des bavures... On verra bien !
Sans attendre de retirer le scotch, un premier enseignement : on n'ébonise pas une surface verticale, à moins de vouloir l'éboniser entièrement !
Le déscotchage de l'assemblage C, initialement traité au même protocole, permet d'en tirer quelques enseignements :
- ça bave sous le scotch par endroits. Un problème de pression de collage ?
- ça migre par capillarité longitudinalement dans les fibres. Comme c'est dans les creux (contrairement à l'ébonisation classique), ça va être galère à corriger...
- il est difficile de déterminer les limites entre pièces au toucher (même avec une pointe/lame) une fois les reprises de surface effectuées. C'est propre mais ce n'est pas sur le trait...
Il va falloir reprendre tout ça sans détériorer l'état de surface. C'est pas gagné...
On en retient au minimum qu'un scotch transparent ou translucide aiderait à la découpe.
L'impact de la colle déposée par l'adhésif sur le bois sur la finition à l'huile est inconnu à ce stade.
Après déscotchage, l'assemblage B présente moins de défauts de teinte que le C.
On retrouve toutefois les mêmes manques, dûs à la difficulté de détourer les pièces derrière un scotch opaque. C'est néanmoins plus facile à corriger que des bavures.
Bilan (provisoire) pour l'assemblage B : l'ébonisation après application d'un adhésif de masquage permet une bonne délimitation entre les pièces, à condition de s'appliquer au collage du scotch et au détourage des pièces.
Le dépoussiérage révèle ce que mes mains avaient déjà constaté : la couleur produite par l'ébonisation ne tient pas par elle-même, et nécessite d'être fixée. Il n'est pas impossible que cette poussière soit simplement de la poussière de ponçage pas nettoyée et ébonisée avec la pièce, mais j'observe des pertes de teinte notables après application des doigts.
Après huilage de l'ensemble de l'assemblage (R***o oil+2C pure), aucune trace de bavure des surfaces ébonisées sur les surfaces vierges. Ouf !
Le résultat est plutôt satisfaisant. Un œil averti le nez sur l'assemblage détecterait la supercherie de la teinte "artificielle", mais à distance normale pour un quidam, l'illusion est suffisante.
Assemblage C : Huilage sélectif avant ébonisation
La logique de ce protocole est que l'huile se lie en surface au bois et forme une barrière à la solution d'ébonisation. Une sorte de scotch de protection liquide, quoi ! L'eau et l'huile ne se mélangeant pas facilement, la limite devrait être bien délimitée, sans risques de bavures.
Vous ne voyez rien ?
Normal, j'ai pris en compte mon retour d'expérience sur l'assemblage B et fait le masquage des surfaces à éboniser plus tard avec un scotch transparent hyper high-tech : du scotch de bureau !
Le huilage a été fait dans la foulée, rien à signaler pour l'instant, si ce n'est qu'il est beaucoup plus facile de suivre un tracé derrière un scotch transparent qu'un scotch opaque, et que la transparence aide à vérifier le bon placage du scotch en tout point.
À noter que les contrequeues étaient initialement ébonisées et ont été poncées pour retrouver une couleur plus normale. On observe que le bois de bout n'a pas récupéré toute sa couleur d'origine, preuve d'une pénétration plus en profondeur de la solution d'ébonisation. Logique, mais tout de même intéressant à noter.
Après ébonisation, le comportement répulsif et protecteur de l'huile vis-à-vis de la solution d'ébonisation est confirmé.
Le résultat est encore une fois satisfaisant, même si on décèle (de très très près) de légères marques noires, qui doivent s'expliquer par le fait que la protection huilée doit comporter quelques défauts.
Cela dit, aucune bavure d'huile sous le scotch n'est à déplorer. Est-ce dû à la nature de l'huile, sa fluidité, son mode de mise en œuvre ou au scotch ? Mystère...
En tout cas, l'usage du scotch de bureau pour la protection est validé. Le risque principal est d'oublier un petit morceau au retrait avant ébonisation. Rien d'impossible à rattraper, de toute façon.
Bilan comparatif
Les essais (et accessoirement le meuble qui les hébergeait) étant terminé, voici venue l'heure du bilan.
Commençons par le point positif commun à tous les protocoles : chaque assemblage donne un résultat visuel satisfaisant. Pourquoi ? Car l'ébonisation tend à masquer les défauts du bois, et ceux des assemblages également.
L'aspect tactile est moins agréable sur l'assemblage A, dont la reprise des bavures au ciseau a altéré l'état de surface général en soulignant les limites entre pièces. Les assemblages B et C sont identiques sur ce point, et probablement similaires à si les pièces n'avaient pas été ébonisées et le huilage fait en deux fois.
À résultat "égal", les protocoles se distinguent tout de même en termes de complexité de mise en œuvre, en particulier au niveau du huilage.
J'ai utilisé du Rubio oil+2C pour faire la finition, soit une huile associée à un durcisseur dont le mélange a une durée de vie limitée. N'appréciant pas la couleur du chêne huilé au Rubio pure (ou à l'huile de lin), je préfère utiliser la nuance "Soupçon de blanc" (White 5%) qui conserve mieux la couleur d'origine du bois brut. Le "soupçon de blanc" est composé d'huile et de pigments blancs, qui ont tendance à remplir les creux du bois (à la manière d'une céruse), contribuant à l'éclaircir.
Hors de question d'utiliser cette nuance sur une pièce ébonisée, ça irait à l'encontre de l'effet recherché.
La finition est donc faite avec 2 huiles différentes selon la couleur. Et en réalité, les assemblages sont huilés à l'huile incolore, et les pièces constitutives hors zone d'assemblage chacune dans leur couleur.
L'assemblage A a nécessité 1 huilage de chaque couleur, d'abord pièce ébonisée + assemblage puis pièce couleur naturelle.
L'assemblage B a été fait en même temps et a nécessité les mêmes opérations dans le même ordre.
L'assemblage C, par contre, a obligé à intervenir en 3 étapes de huilage. Ça paraît minime, mais pour ce type d'huile, ça implique temps de préparation, perte de produit et de consommables et temps de séchage intermédiaire.
Au vu de la qualité comparée des assemblages B et C, l'ébonisation sélective avant huilage (assemblage B) me semble un bon compromis, même si un huilage sélectif préalable (assemblage C) permet d'avoir plus de sécurité à l'étape de l'ébonisation.
Pour ce type d'exercice, et de façon inattendue, le scotch de bureau transparent s'est révélé être un bon candidat, à la fois par sa protection, l'absence perçue de résidus de colle, et évidemment par sa transparence qui facilite le détourage des pièces, mais aussi le contrôle du collage sur la pièce.
Une utilisation de la même huile sur toutes les pièces rend les protocoles B et C équivalents en nombre d'étapes, et rend donc préférable le huilage sélectif préalable (assemblage C) pour sa plus grande sécurité de réalisation.
Discussion autour de la place du collage dans le protocole
Une remarque récurrente sur ma démarche a porté sur la place du collage dans l'ordre des opérations à réaliser. Il semble en effet logique de teinter séparément les pièces, voire de les huiler, et de les assembler seulement ensuite.
Cette démarche est valable pour les assemblages masqués, pour lesquels les défauts d'alignement sont moins critiques. Mais pour un assemblage visible de type queues (droites ou d'aronde), il est d'usage (?) de tailler ses queues légèrement trop longues pour mieux affleurer au rabot la surface de l'assemblage afin d'avoir un aspect et un toucher "parfait". Il serait théoriquement possible de faire cette opération lors d'un montage à blanc, puis de démonter l'assemblage, de teinter les pièces et réassembler pour coller en position définitive.
Trois problèmes me semblent liés à ce protocole :
- je ne me sens pas capable de repositionner au 1/20e de millimètre près l'assemblage dans sa position de montage à blanc, a fortiori avec de la colle, qui a une épaisseur.
- la colle doit baver (un peu) en-dehors de l'assemblage. Ces bavures doivent être nettoyées. À l'éponge humide, elle s'étalera sur les pièces, et bloquera la pénétration de l'huile. À sec, elle devra être enlevée au racloir ou au ciseau, occasionnant forcément un léger retrait de matière dans l'assemblage.
- l'épaisseur effective d'une ébonisation au pinceau est à la fois très fine et très fragile. Un passage de rabot ou de racloir met quasiment le bois à nu. De ce fait, toute reprise de surface après ébonisation est impossible sans altérer la teinte.
Du fait de cette très faible épaisseur de réaction d'ébonisation, le figeage de la géométrie de l'assemblage avant mise en teinte est impératif.
Augmenter la profondeur d'effet de la réaction pourrait permettre de changer l'ordre des opérations, mais ce n'est pas possible avec une ébonisation au pinceau.
Parmi les méthodes susceptibles d'augmenter cette profondeur, l'ébonisation par immersion ou par imprégnation sous vide. N'hésitez pas à vous lancer dans des expérimentations afin d'améliorer ce protocole d'ébonisation sélective pour les assemblages (visibles).
D'ici-là, j'espère que ce pas-à-pas vous aura apporté quelque chose et vous incitera à vous lancer dans l'aventure.
Discussions
merci pour ce pas à pas. hâte de lire la suite.
Merci gerald1981 de m'avoir poussé à le rédiger
Salut Yougzz, il me semble que nous en avions parlé mais j'ai un doute, il serait intéressant de coupler une des méthodes au traitement préalable de la partie claire pour ne pas que l'ébonisation réagisse. Quoi qu'il en soit, ça reste le même problème : Passer le traitement sur la partie claire sans baver ou toucher les parties que l'on souhaite éboniser... Merci pour ce pas à pas.
Salut JB4WOOD ,
En effet, c'est toi qui a inspiré le protocole de l'assemblage C
J'attends de l'huile monocouche d'une marque bien connue pour faire l'essai (je n'ai que du soupçon de blanc en stock, ça aurait fait tâche sur les pièces ébonisées...).
Je n'ai pas de solution à ce jour pour découper précisément le scotch de protection juste sur les limites de pièces
Interressant ! As tu tenté d'eboniser avant de coller l'assemblage ?
Salut benjams,
La question m'a été posée par ailleurs, la réponse courte est non, mais j'ai prévu un article expliquant pourquoi. À venir très bientôt
Yougzz
En imprégnant bien la pièce avec une solution tannique et plusieurs applications d'oxyde de fer comme décrit ici
Il y a aussi des zones qui prendront jamais la teinte sur certains bois comme ici :
Très intéressant ton pas-à-pas, merci de me l'avoir signalé !
Effectivement, même avec un ajout de tanins, le bois réagit différemment selon les zones. Mais je trouve que c'est ce qui fait l'intérêt, sinon autant passer une peinture !
J'essaierai d'ajouter de l'alcool à ma solution la prochaine fois (si j'y pense...)