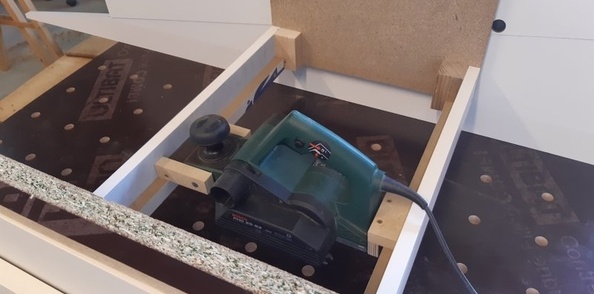
Qui n'a jamais eu besoin de raboter plus large que sa raboteuse ? Les puristes me diront "ha ha moi je fais tout à la varlope !", mais moi je préfère utiliser la fée électricité, chacun son truc !
Ce type de montage d'usinage a déjà été largement fait et refait, en particulier avec des rails et un chariot qui supporte une défonceuse. Exemple :
Il y a quelques conceptions plus originales, comme celle-ci qui me plaisait beaucoup...
...mais qui a deux inconvénients majeurs dans mon cas :
- il faut un système pour maintenir la planche à dégauchir (or je n'ai pas d'établi de menuisier ni de presse sur pied ou latérale),
- j'envisage de dégauchir des planches très voilées, et ce système me parait limité à 1 passe de rabot électrique, donc 2,5mm max.
Pour autant, j'aime l'idée d'utiliser un rabot électrique plutôt qu'une défonceuse...
Liste des articles
Éléments de conception
Déjà, pourquoi utiliser un rabot électrique plutôt qu'une défonceuse ?
D'une part pour l'état de surface qui devrait être meilleur, d'autre part pour faire le travail beaucoup plus rapidement. En effet, si l'on compare un rabot électrique avec un fer de 82mm (et disons qu'on fasse des passes de 72mm) avec une défonceuse équipée par exemple d'une fraise DN20 :
Soit on fait des passes de 9mm, uniquement vers la droite pour travailler en opposition (et gare si on se trompe de sens !), et ça fait 8 fois plus de passes qu'au rabot.
Soit on fait des passes de 18mm (et dans ce cas on peut se permettre de faire des passes vers la droite et vers la gauche), mais la fraise va vouloir partir de biais donc en pratique il faudrait bloquer le chariot. Cela nécessite un système supplémentaire et fait perdre du temps.
Par contre j'ai bien compris l'intérêt de la défonceuse par rapport au rabot électrique : on la pose dans le chariot et l'outil descend vers la pièce de bois à usiner. Quand on veut faire une passe supplémentaire, on descend la fraise de quelques millimètres et on recommence (donc aucun réglage à faire sur le montage d'usinage).
À l'inverse, le fer du rabot électrique ne peut pas descendre au dessous du chariot, et à chaque passe il faudra faire un réglage du montage d'usinage.
Il faut donc une table de dégauchissage avec les caractéristiques suivantes :
- Permettre de fixer la pièce de bois à raboter en laissant toute la surface disponible,
- Maintien du rabot électrique à plat,
- Réglage de la hauteur du chariot par rapport à la table,
- Robustesse du parallélisme du chariot par rapport à la table,
- Indice PSTM élevé pour le réglage de hauteur.
Voici mon rabot :
Et voilà comment je compte m'y prendre :
Le support sera une table de type "MFT" (pleine de trous régulièrement espacés pour y planter des taquets de serrage de la planche à usiner)
Les deux rails latéraux seront réglables en hauteur
Le chariot sera "simple" (sans réglage) et glissera (facilement) sur les rails
Le rabot sera adapté pour aller dans le chariot dans lequel il glissera latéralement (pas facilement).
Contrairement à une table de rabotage pour défonceuse, ici les passes se feront de l'arrière vers l'avant, puis on décalera le rabot et on recommencera. Il faut donc que le chariot glisse facilement sur les rails, mais que le mouvement latéral du rabot soit plus difficile et ainsi avoir des chances que ça tire droit.
L'adaptation du rabot
Je commence par la fin parce que c'est le rabot qui déterminera les dimensions du chariot (puis c'est le chariot qui déterminera les dimensions du système de rails, puis c'est les rails qui détermineront le positionnement de la première ligne de trous "MFT").
Nous avons donc 3 filetages, deux latéraux à l'avant (hauteur 41,5 mm par rapport au sabot), et un, plus bas, à l'arrière (13,5 mm).
Mon objectif est de créer des sabots qui viendront en "épaulement" sur le chariot, permettant au rabot d'y être suspendu. Et plutôt que de prévoir un chariot asymétrique, je préfère qu'il soit simple, et pour cela mettre les sabots à la même hauteur malgré la différence de hauteur des filetages.
Voilà le sabot avant :
J'aurais préféré faire les trois pièces en MDF mais ça se fend quand on visse dedans, donc la partie du milieu est en CTP. À noter que l'ensemble a un degré de liberté en rotation, mais par chance la pièce du milieu en CTP vient se caler sur un petit rebord du plastique, donc c'est à peu près horizontal.
Ensuite, l'important sera d'avoir la même hauteur (ici, 29mm) sur le sabot arrière qui n'est qu'une petite équerre.
À noter que là aussi il y a un degré de liberté en rotation (en roulis) puisqu'il n'y a qu'une vis et pas de blocage en position. Je vais cependant le laisser ainsi sans trop serrer la vis, cela permettra d'avoir un montage isostatique, ce n'est pas plus mal.
Par contre petit aléa...
La carcasse n'est pas d'équerre, si bien que mon sabot est de biais. Et la hauteur prévue (29mm) n'est plus respectée.
Quelques solutions possibles : mettre une cale pour rattraper l'angle, laisser l'angle mais abaisser l'ensemble pour revenir à la cote, donner un coup de rabot (à main) pour que la pièce épouse la forme de la carcasse...
Je vais cependant attendre d'avoir fait le chariot pour voir si cela pose problème ou pas. Rappelons-nous que l'objectif est d'avoir un rabot à l'horizontale pour qu'il puisse usiner la planche. Mais c'est surtout ses mouvements qui doivent être parallèles au plan de travail, sa "posture" est moins importante.
Voici le résultat une fois monté :
La fabrication du chariot
Le chariot est au départ tout simple (enfin le diable se cachant dans les détails, dit-on, il est moins simple que prévu !).
C'est un cadre.
Avec deux épaulements à l'intérieur (pour y faire glisser le rabot), et deux épaulements à l'extérieur (pour le translater sur les rails).
- Sa largeur fait la même largeur que la planche MFT moins deux fois l'épaisseur des rails,
- Sa longueur fait la longueur du rabot, sabots compris, plus deux fois l'épaisseur des montants.
En effet j'ai décidé que le rabot serait guidé par les montants, avec du jeu au niveau des épaulements. Petit schéma pour mieux comprendre.
Le rabot est schématisé en vert (vu de profil), les sabots que j'ai constitués sont en orange et les montants + épaulements en bleu.
Il faut cependant que le cadre soit un peu contreventé pour éviter qu'il se mette en travers, ce qui pourrait empêcher la translation latérale du rabot, ou gêner son parcours longitudinal sur les rails.
Au début j'ai eu l'idée de mettre des petits triangles dans les coins, mais comme j'utilise du MDF, celui-ci va se fendre. J'ai alors pensé mettre du vrai bois (une chute de planche à plat), mais d'un côté il sera vissé dans l'about, je n'aime pas trop cela. D'autre part il faut aussi fixer les planches du cadre ensemble, et là encore c'est du MDF... et même avec les vis SPAX spéciales MDF il faut bien plus de largeur pour éviter que ça ne se fende.
Donc au final, je veux visser dans du vrai bois, dans le sens du fil des deux côtés et sur toute la hauteur du cadre => petit carrelet vertical. Et j'ai retaillé les épaulements qui gênaient.
Ça donne ceci.
Et avec le rabot en position :
À noter que les carrelets ont été choisis en fonction de l'espace disponible pour perdre le moins de déplacement possible...
Bilan : ça marche.
Mais.
Contrairement à ce que je pensais, je ne pourrai pas faire les rails comme je voulais en fonction des dimensions du chariot. Je vais donc devoir adapter le chariot à la hauteur des rails et non l'inverse, mais ça c'est une autre histoire...
La fabrication de la table
Finalement je me suis dit qu'il serait plus simple de faire la table avant les rails, alors c'est parti.
Je ne connais pas les dimensions standard des tables MFT, alors j'ai pris ce que j'avais :
- deux chutes de CTP filmé de 15, de 1250 x 690
- 1 m de tourillon 18
J'ai choisi un pas de 100 mm et je m'économise une ligne de trous de chaque côté car il est peu probable qu'ils soient utiles.
Mais d'abord, fixer les deux plateaux l'un sur l'autre pour avoir 3cm d'épaisseur (sinon les taquets prendront très vite du jeu...).
Et après avoir tracé le réseau de trous, une quinzaine de vis réparties un peu partout pour que les deux plaques soient bien maintenues sur toute la surface.
Pour le perçage, une mèche plate et deux perceuses (pour alterner parce qu'elles souffrent !).
Pas de guidage, la verticalité est faite "au talent" (comme disent les jeunes, moi je dis "au pif" !). Ma méthode (un poil meilleure que le pif) : je me place derrière la perceuse et je cale la mèche verticale par rapport au sens [droite - gauche], puis je place ma tête à gauche de la perceuse et je cale la verticalité [avant - arrière], je reviens derrière la perceuse, petit coup d'oeil pour voir si ça n'a pas bougé [droite - gauche] et je perce.
Autre moyen de contrôle, au premier tour de mèche si c'est droit je dois avoir ceci :
Si c'est plus usiné d'un côté que de l'autre, je recale pour avoir un disque homogène.
À noter que la parfaite verticalité n'est pas vraiment nécessaire : si un trou est décalé par rapport aux autres ou s'il n'est pas bien vertical, ça n'empêchera pas de serrer la planche à usiner.
Après chaque trou je rafraichis la mèche dans un seau d'eau, j'aurais de l'huile de coupe je l'utiliserais mais l'eau va bien aussi.
Et donc au final voici le recto...
Et malgré l'utilisation d'une planche martyr, le verso n'est pas fifou... beaucoup d'arrachements, mais là encore ce n'est pas bien grave, ça ne se verra pas.
La conception des rails
La clé de cette table d'usinage, c'est les deux rails latéraux qui vont porter le chariot. Pour rappel, le cahier des charges est le suivant :
- Réglables en hauteur avec un indice PSTM élevé
- Fiables (parallélisme garanti)
- Robustes (une fois réglés, ils ne doivent plus bouger et ils ne s'affaissent pas au passage du chariot)
- Avec un débattement de 60 mm, j'ai dit !
Pourquoi 60 ? Parce que je considère que je ne dégauchirai pas de planche de moins de 20 mm, ni des planches de plus de 80 mm. Entre les deux je veux pouvoir faire ce que je veux.
Et là, ça se corse.
Voici le principe que j'envisage :
Le réglage de la hauteur se fait donc en déplaçant le rail vert sur son plan incliné rouge (qui est fixe) et une vis TRCC fixée au rail vient coulisser dans la lumière de la joue. On peut tracer des graduations sur les plans inclinés pour faciliter le réglage de la hauteur, qui sera d'autant plus précis que l'angle sera faible. Le point n°1 est donc respecté : PSTM élevé.
Les plans inclinés sont posés sur la table. Il n'y a pas mieux pour garantir leur planéité et absence de déformation. Bien sûr ils seront coupés les deux ensemble pour garantir l'angle identique des deux côtés. Les rails (la partie verte) seront constitués de l'autre partie de la planche coupée en biais, et reposent sur les plans inclinés. Ils ne pourront donc pas ne pas être parallèles => point n°2 respecté.
À part un ou deux trous pour passer les vis TRCC, ils sont intègres donc indéformables aussi. Au départ je pensais faire la rainure dans les rails mais elle fragilise l'ensemble, donc autant les faire dans les joues. Point n°3 respecté.
NB : les joues sont bien grandes pour peu de chose, mais elle servent à guider les rails et maintenir les plans inclinés en place.
Reste le point n°4 à respecter : débattement de 60 mm.
Tel que dessiné, l'ensemble [plan incliné + rail], dans sa position neutre, fait 100 mm de haut (les 60 + 20 de marge en bas et 20 en haut). Et pour monter les rails de 60 mm, il faut les tirer vers l'arrière d'à peu près la moitié de leur longueur...
Mais dans ce cas, la zone d'usinage ne recouvre plus que la moitié de ma table MFT, à moins de faire des joues amovibles qui puissent s'avancer, mais ça complique pas mal les choses... En rédigeant cet article, je me rends compte qu'une solution plus élégante serait de faire les plans inclinés amovibles, avec une seconde lumière, cette fois horizontale, dans les joues.
Cela permettrait d'avancer d'autant les plans inclinés que je recule les rails.
Bon... on voit que ça se complique pour faire tenir les rails (cela reste possible avec un autre système de rainures et des joues plus hautes) mais le déport des pointes des rails ne respecte plus le critère de robustesse.
Donc pour bien faire, il faudrait que les triangles aient un angle plus prononcé. Par exemple avoir mon débattement de 60 mm pour un déplacement de 300 mm, parait raisonnable...
Mais alors comment faire ? Si je taille mes planches au bon angle, je n'ai plus assez de longueur...
Donc là j'ai commencé à imaginer faire deux joues en triangle de chaque côté et un rail qui vient se fixer sur la partie mobile, plus un système de fixation par rainure dans une 3ème joue etc. (l'indice PSTM baisse, baisse, baisse...). J'ai vite abandonné cette option mais je montre ce que ça donne au cas où certains rebondiraient sur l'idée... sait-on jamais !
(les trois planches vertes sont solidaires, en principe ça respecte toutes les conditions)
En tout cas j'ai fait plus simple : des triangles de la bonne longueur (1200 mm), ET du bon angle, donc simplement plus hauts !
Voici donc le schéma de la conception finale : des triangles de 1200 de long et 280 de haut, avec un angle de 60 / 300. Les joues sont également plus hautes. Le rail au premier plan est positionné au maximum de la hauteur voulue (+60mm par rapport à l'autre) et on voit que la surface utilisable pour l'usinage reste acceptable.
Mais pour le coup ça oblige à revoir le chariot qui doit avoir des flancs beaucoup plus hauts pour que le rabot soit à la bonne hauteur.
La construction et l'optimisation des rails
Une fois la conception trouvée, reste à réaliser les rails avec les matériaux disponibles. Or, j'ai des grandes plaques de récupération en MDF de 19 avec des largeurs variables mais de longueurs identiques : 2460 mm. Et ma table faisant 1200, on peut se dire qu'avec une longueur de plaque je peux faire deux paires de triangles de 1200 avec une chute de 6 cm, c'est peu coûteux et optimal.
Mais... cela ne serait-il pas un peu trop simple ? Il ne faudrait pas non plus exploser l'indice PSTM ! Donc pour compliquer un peu les choses, j'ai choisi de couper la plaque en deux parties inégales. Car n'oublions pas qu'il y a aussi les joues à faire (en principe 2 x 1200 aussi).
Or, les joues peuvent être un peu plus petites que les triangles, ça marchera aussi. Et plus les triangles sont longs, mieux c'est. Donc dans une longueur de plaque de 2460, je coupe 900 pour une joue et 1560 pour une paire de triangles qui dépasseront de la table, ce qui n'est pas plus mal. Au contraire, par un effet d'aubaine pas tout à fait prévu, cette dimension est génialissime !
Voici le montage final sans les rails :
L'arrière des plans inclinés sont à fleur de la table, les pointes dépassent de 35 cm. Ils sont fixés aux joues par 4 vis qu'on aperçoit sur la photo.
Voici le montage final avec les rails, celui en avant-plan étant reculé à fond, et on remarque qu'à l'avant il vient à fleur de la table.
Et c'est ça qui est génial, car quelle que soit la hauteur choisie, les rails couvrent l'ensemble de la table.
Quelques détails constructifs pour ceux que ça intéresse. Les perçages dans les joues (avec des vis en zig-zag pour aller dans les deux plaques de la table, mais au final les joues ne sont quand même pas très verticales...).
Détail des usinages pour les vis TRCC (à noter que, comme je le pensais, il n'est absolument pas nécessaire de les serrer avec une clé : un simple serrage à la main et le rail ne bouge plus !) :
Les pions de maintien en position :
Le chariot avec ses nouveaux flancs beaucoup plus hauts :
Et maintenant, plus qu'à l'essayer !
Premier essai
Bah, ça marche...
...mais pas trop bien.
Déjà, j'ai fait l'essai sur une planche de 350 x 350 assez tuilée : j'ai mis 1/2h temps métal pour faire la première face, certes il a fallu enlever 9mm d'épaisseur en tout (par passes d'environ 1 mm) mais ça me parait hyper long quand même. Vingt minutes pour la seconde face (où j'ai enlevé 4 mm), c'est très long aussi.
NB : Le risque de kick-back n'est pas nul, donc à l'usinage il est bon de lever légèrement le talon du rabot quand on le ramène.
Ensuite l'état de surface est déplorable pour deux raisons : le rabot plonge sur le côté gauche (d'où les stries). Pourtant j'ai contrôlé toutes mes cotes sur le rabot, le chariot et les rails, toutes semblent bonnes. C'est incompréhensible mais j'ai pu repérer que le problème vient du rabot car si je le change de sens les stries sont toujours sur son côté gauche.
D'autre part la surface monte quand j'avance, si bien que j'ai changé le sens du rabot pour aplanir l'autre côté de ma planche. Conclusion c'est plein de stries et ce n'est pas plan ! Il faut bien l'avouer, le résultat est très très en-deçà de la qualité escomptée.
Pour le coup tout n'est pas négatif : il n'empêche que ça me fait une ébauche utilisable pour ensuite être passée à la ponceuse calibreuse. Je m'en sors donc honorablement même si intrinsèquement la table n'est pas au niveau.
On va dire que les fous furieux de la varlope ont encore de beaux jours devant eux !
Maintenant essayons de comprendre pourquoi ça ne marche pas.
Les stries d'1 mm sur le côté gauche du rabot, c'est qu'il a du roulis donc que la cale du devant n'est pas horizontale. Dans l'idéal il serait bon d'avoir une vis de réglage...
Pour le fait qu'il monte, il se pourrait bien que cela soit lié à la cale de derrière qui était, rappelons-le, un peu trop haute à cause de l'angle pas tout à fait droit de la carcasse. Or si la cale est trop haute, l'arrière du rabot est trop bas, donc il monte, CQFD.
Quant au degré de liberté en rotation de la cale arrière, cela semble ne pas gêner, au contraire. Je ne vais donc pas essayer de faire mieux sur ce sujet.
Second essai
Alors correction n°1 : le sabot arrière. Retaillé d'un millimètre et tant qu'on y est recoupé de biais (au pif 2,5°).
NB : en écrivant l'article je me rends compte que j'ai oublié de remettre l'angle de la scie à 90°... si j'oublie de le remettre ça va faire un malheur, vous me le rappellerez ?
Correction n°2 : j'avais imaginé une vis de réglage PSTM 4 mais j'ai préféré un [rien de] réglage PSTM 8. Dévisser de quelques tours, désaffleurer dans le bon sens à la main en utilisant le jeu disponible, revisser et go, on verra bien ce que ça donne.
Et pis c'est tout ! Pas que je sois tenace mais... si la logique veut que quelque chose se passe d'une certaine manière, la réalité n'a qu'à s'y plier, voilà tout !
(Après, des fois je me plante dans la logique, mais c'est un autre sujet !)
Et donc second essai.
Résultat en lumière rasante :
Franchement pas mal, non ?
Et au verso pareil, sachant que j'ai pris soin de tourner la planche dans le sens droite-gauche et non dans le sens avant-arrière. De cette manière, si le chariot est légèrement de biais (et donc la surface aussi), les deux surfaces resteront parallèles.
Alors j'avoue que j'ai quand même retourné le rabot et usiné dans l'autre sens, et ça enlevait des copeaux (ce qui laisse penser que le rabot monte encore). En tout cas en posant une règle dessus, on voit que la surface est loin d'être nickel, mais elle est tout à fait acceptable avant ponçage. Plus de stries et plus d'effet bombé.
Je ferai d'autres tests pour mesurer la précision, mais d'ores et déjà la table peut entrer en production.
Et après, et après...
Et après, ça marche.
Plutôt bien.
Retour d'expérience
Temps d'usinage
C'est long. Pour une planche bien tuilée de 50 cm de long et 35 de large, ça me prend 30 min pour environ 15 passes (donc 15 réglages des rails, même si c'est rapide, ça dure). Je ne sais pas si c'est plus rapide pour ceux qui ont un chariot pour défonceuse...
Je fais 1 mm par passe, et finalement le rabot n'est pas assez puissant pour prendre le millimètre sur toute la largeur des fers (82 mm). Donc je ne fais l'usinage que sur la moitié des fers.
Réglage des rails
La hauteur des rails n'est pas très "plus simple tu meurs" à régler. J'ai tracé des graduations au critérium mais elles s'effacent petit à petit sous les frottements du MDF. D'autre part, il faut quand même forcer un peu pour mouvoir le rail, et à ce moment là il part d'un coup donc il faut le faire revenir en arrière vers la bonne graduation par petites "claques techniques". L'idéal serait d'avoir un petit étrier qu'on visserait à la bonne graduation (qui ferait butée), puis on tirerait le rail jusqu'à l'étrier. Ça reste à inventer.
Travail de la surface
Le rabot ayant un mouvement longitudinal avec ses fers transversaux, ça a tendance à taper. Dans l'idéal ça aurait été bien que le rabot avance en crabe, mais je ne vais pas refaire le montage d'usinage pour ça. Si quelqu'un veut s'y coller, je pense qu'en inventant des sabots adéquats, on devrait pouvoir le faire avancer en crabe en conservant tout le reste de la table de rabotage. Je lance le concours interne !
Aléas
Il arrive que la passe soit plus profonde que prévu... quand la planche s'est décollée de la table de travail ! Cela arrive quand le rabot broute sur un nœud par exemple, ou dans une zone plus dure ou si ma passe est trop large. Dans ce cas les vibrations font remonter la planche et il faut s'astreindre à arrêter le travail, aspirer les copeaux, enlever les coins de fixation et refixer la planche.
Posture de travail
Au début je tenais le rabot d'une main et le chariot de l'autre. Depuis que je tiens le rabot à deux mains (le chariot suit !), l'état de surface est meilleur.
Évacuation des copeaux
Les bons menuisiers ont de bons aspirateurs. Pas moi. L'aspirateur à copeaux de la machine à bois n'est pas adapté, donc actuellement je mets des copeaux partout et toutes les deux passes je les aspire. Je ne crois pas nécessaire d'inventer un truc genre "caisson fermé avec aspiration incorporée", ça complique beaucoup trop la chose. Il faut juste avoir un aspirateur qui prend les copeaux à la source. Ça limite un peu la largeur utile de la table puisqu'avec le tuyau le rabot ne pourra plus aller contre le bord, mais c'est le prix à payer pour travailler proprement.
État de surface
Pas génialissime, soyons clairs : c'est mieux d'avoir une raboteuse de 410 ou de (bien) travailler à la varlope. Vu de près ça fait des vagues de 1 ou 2 dixièmes à peu près. Pour moi ça reste acceptable parce qu'après la planche passe à la ponceuse calibreuse.
On voit d'ailleurs que le rabot plonge toujours un peu à gauche... c'est les limites de mon réglage du talon au pifomètre !
Améliorations
J'ai encore 8 planches à faire... 4 heures de boulot, je vais mourir ! Mais je ne remercierai jamais assez benjam de m'avoir soufflé l'idée que...
Quelques coups de rabot électrique bien placé à l’œil est c'était mieux
Eh oui pourquoi pas commencer "au talent" et quand l'ébauche est faite, finir avec le chariot ?
Et là, je peux y aller de biais par passes de 0,5mm sur toute la largeur des fers, ça tape moins et surtout c'est hyper rapide parce qu'il n'y a pas besoin de régler les rails à chaque fois.
Le premier essai était encourageant, avec cette méthode je pense diviser le nombre de passes par deux (donc plus que 15 min par planche) + environ 5 minutes pour l'ébauche = 20 minutes au lieu de 30, je gagne 1/3 de temps d'usinage.
(à confirmer)
D'autre part, le rabot a plus de 20 ans et je n'ai jamais changé les fers... Je ne l'ai jamais utilisé de manière intensive, mais quand même ça mérite ! Et ça devrait aller plus vite, moins taper, chauffer moins... que des avantages !
(à suivre)
Au final, le bilan !
La méthode améliorée qui consiste à dégauchir le plus gros à vue et finir au chariot fait gagner un petit peu de temps mais pas beaucoup (25 min au lieu de 30).
Avoir des glissières fartées (un coup de paraffine ou de savon sec dessus) rend le travail bien plus plaisant et efficace. De même, contrairement à ce que j'avais pensé au début (cf. cahier des charges), le fait d'avoir des glissières latérales bien glissantes (pour le mouvement droite / gauche du rabot) est bien meilleur et ne génère pas de mouvements intempestifs. Si c'était à refaire je les ferais en CTP filmé plutôt qu'en MDF.
Avoir des fers neuf m'a changé la vie ! Je peux prendre des passes de 3/4 de la largeur des fers (voire le fer entier) sans que ça ne broute, et c'est un vrai plaisir d'avancer le rabot avec.
Pour les écrous carrés des vis TRCC, ça marche mais une manette ou un système à excentrique comme sur les moyeux des vélos serait toutefois plus pratique.
Les trous "MFT" espacés de 10 cm, il ne faut pas plus ! Un pas de 7,5 cm aurait même été un peu plus pratique.
La table de 68 cm de large sur 120 de long permet en théorie d'usiner des planches jusqu'à 49 cm sur 98 (avec mon rabot). En pratique c'est adéquat pour un travail jusqu'à 35 cm de large et plutôt 80 de long. Cela me convient bien pour l'usage que j'en ai : faire des planches à découper.
Si besoin de plus large, il est possible d'élargir l'ensemble (table et chariot), la limite étant liée à la rigidité du chariot pour qu'il ne s'affaisse pas au milieu du travail.
Si besoin de plus long, ça se complique car pour garder le même principe de rails triangles avec un angle de 60 / 300 (60 mm de débattement vertical quand on tire les rails de 300 mm), il faut encore augmenter la hauteur des rails. Pour une table d'1,20 m les rails font 24 cm de haut, si on double la longueur, on double la hauteur des rails ce qui coûte beaucoup de panneau et rend l'ensemble lourd, encombrant et peu maniable. Donc dans ce cas mieux vaudrait partir sur la conception à laquelle j'avais renoncé (rails fixés à deux "petits" triangles et joue pour le maintien en position).
Avec cette conception, on peut faire une table de la longueur qu'on veut tout en conservant des rails de hauteur raisonnable (indépendante de la longueur). Et un chariot de hauteur raisonnable aussi.
Cela évite également d'avoir des pointes qui dépassent... Au final, cette conception est probablement la meilleure !
La concurrence...
Je ne mets que la concurrence pour des systèmes avec rabot électrique. Si vous en trouvez d'autres n'hésitez pas à me les indiquer, je les ajouterai ici.
Comme indiqué en haut : le chariot à mouvement polaire de LionelDraghi
Une vidéo de JSK-koubou (merci bntarc) : 3 in 1 Hack an electric hand planer jigs
Discussions
Bonjour,
je vais suivre ton projet avec attention. J'avais choisi un rabot dans cette perspective, me restait à faire "la table"…
Tant mieux si ça peut te donner des idées (et éviter les soucis que j'aurai eu).
Je ne publierai pas le plan car (déjà il n'y en n'a pas !) c'est un montage à faire vraiment sur mesure en fonction de ton rabot et de ton cahier des charges. Mais si besoin je mettrai les cotes que tu veux dans les commentaires.
Question pour les trous de fabrication de la table: c’était aussi faisable à la défonceuse, non ?
Ou bien il faut absolument un rail perforé et toute une panoplie d’accessoires couteux pour cette méthode ?
Du bon scotch de peintre n’aurait pas suffit à éviter les éclats au verso du plateau ?
Travailler au talent, c’est la base :D
Hâte de lire la suite !
À la défonceuse oui, mais il faut une fraise ad hoc, il faut un rail, et il faut quand même marquer les trous pour savoir où les faire...
Bravo pour ta recherche du PSTM ;)
Pour éviter les éclats en sortie des trous, tu aurais pu arrêter les perçages dès que la pointe traverse et reprendre par l'autre côté. Mais c'est plus long.
Oui tu as raison, mais les deux cylindres percés ne sont pas forcément très bien alignés et ça peut donner un cran à l'intérieur.
Dans mon cas la seule chose importante du point de vue fonctionnel, c'est d'avoir le moins de jeu possible au niveau des taquets donc des trous propres. Alignement, angle et bien sûr esthétique passent après.
Ou alors "contrepercer" juste le dernier millimètre aurait pu être une bonne idée...
Je n'ai jamais remarqué de cran, mais tu as raison.
En fait, je ne m'arrête pas à 1 mm, plutôt 2 ou 3.
Bonne idée!
Pour le réglage en hauteur, on pourrait faire un cadre sur un double plan incliné. En avançant/reculant le plan incliné supérieur, on peut faire varier la hauteur (comme pour le réglage des tables d'une dégauchisseuse).
Comme ici:
Bonne idée Kentaro ! D'ailleurs c'est comme ça que j'ai fait
Mais pour le coup entre l'idée et la réalisation... il y a eu quelques difficultés ! Je vais montrer tout ça au prochain article.
Ara Ah d'accord! je n'avais pas tout compris...
Kentaro normal, je ne l'avais pas encore dit !
Je m'y mets ce soir.
Ara Il y a donc eu convergence de (grands) esprits!
Je ne comprend pas en quoi c'est plus simple d'avoir des réglages en hauteur au niveau des rails au lieu de les avoir au niveau du chariot... Si c'est au niveau du chariot (même technique des 2 triangles) ça peut s'adapter à nimporte quelles taille de coupe il me semble...
Bah... je n'y ai pas pensé ! Tu as sûrement raison mais je ne vois pas trop comment faire les triangles au niveau du chariot... Un petit schéma ?
Faut pas pousser mémé dans les orties ;) de là a vraiment penser au design... La même chose que sur les côtés de la planche mais sur les côtés du chariot. Voyons c'est simnple non?
Ben... nan c'est pas si simple ! Tu me fais remplacer ma petite glissière ou mieux : carrément le flanc, par un triangle. Et il pose sur un autre triangle inversé, les deux constituant le flanc. Mais comment ils tiennent ensemble ? Avec une joue comme j'ai fait ? Pourquoi pas mais qu'est-ce que j'y gagne ? Un peu de matière, certes, mais pas de simplicité...
(mais je n'ai peut-être pas tout compris...)
wouain, c'est pas gagné effectivement ;) J'ai pas toujours de bonnes idées ;)
Bon de toute façon, hein, je ne vais pas recommencer pour tes beaux yeux !
(ah, c'est que la clientèle féminine est toujours exigeante !)
J'attends de voir comment ça marche...
Dans mon idée, les plans inclinés ne servent qu'à régler finement la hauteur du rabot (donc, pas très longs, le réglage en coulissement se faisant seulement sur 1 ou 2 cm)) et donc, la hauteur de coupe. Ensuite, l'ensemble coulisse sur des rails horizontaux, comme sur le système avec défonçeuse.
Kentaro oui c'est bien ça, les rails ont un débattement de 350 mm en largeur et de 60 mm en hauteur, après pour chaque passe je les avance de... ben... environ 6 mm pour faire descendre le rabot de 1 mm.
C'est en effet plutôt décevant ! Quelques coups de rabot électrique bien placé à l'oeil est c'était mieux
Par contre, je sur sur qu'il y a moyen de faire quelque chose de bien et que c'est une bonne idée de partir sur un rabot par rapport à un défonceuse.
Comme les autres, je pense que les rails doivent être fixe.
Question, ta table d'entrée de ton rabot est relevé au max et ne touche pas ton bois ?
Oui benjam, la "table" d'entrée était bien relevée de 2,5 mm. Finalement ce n'était qu'une question de réglage de mes (gros) sabots !
Ara Tant mieux. Si un jour j'ai besoin de dégauchir de grande planche, je reviendrais par là.
Penses à remettre à 90° l'angle de ta scie sous table !
Ah oui si tu as besoin tu es le bienvenu aux Ateliers CFC (tu habites tout près d'ici je crois, à un hémisphère près
)
Merci pour l'invite. Je parlais de ton pas à pas ;)
A part les stries, je trouve cela plutôt pas mal.
Il est possible que le montage ne soit pas assez robuste, il doit plier par endroits. Il faudrait peut-être faire cela avec de plus grosse sections, contreventer, etc.
Non Kentaro franchement je ne le vois pas ployer sous la contrainte, d'autant que dans ce cas cela ferait surtout un creux dans la partie médiane de la pièce. Il fallait juste que je sois plus précis sur le montage de mes sabots.
Après, il y a encore quelques optimisations à faire mais c'est une autre histoire !
bon, et bien bravo!
Merci
3 in 1 Hack an electric hand planer jigs / Three amazing bench top jointers
youtube.com/wa...h?v=ko2Tl7cDl6E
Wé, c'est pas mal, son montage n°2 correspond à ma problématique mais j'ai des planches très tuilées (donc besoin de faire plusieurs passes). Le fait d'avoir un système de rails réglables en hauteur est un vrai plus.
On peu imaginer son système sur des rails réglables, c'est apparemment plus simple que mon chariot.
Bonjour, Bonne idée à priori, je pense qu'il doit y avoir moyen de faire un système plus simple, à partir de 2 règles de maçon par exemple, avec un réglage des hauteurs par vis. Par contre il faut garder à l'esprit que sur un rabot électrique, les fers sont à la même hauteur que le plateau arrière, donc à minima il faut prévoir le recul suffisant.